How is bitumen Produced?
Petroleum Bitumen, normally called “Bitumen” or “Asphalt” is produced by refining crude oil. Used as a binder in road-building products, it is a very viscous, black or dark brown material.
The crude oil is pumped from storage tanks, where it is kept at about 60°C, through a heat exchanger system where its temperature is increased to typically 200°C by exchanging heat gained from the cooling of newly produced products in the refining process. The crude is then further heated in a furnace to typically 300° C where it is partly vaporized into an Atmospheric Distillation Column. Here the physical separation of the components occurs. The lighter components rise to the top and the heaviest components (the atmospheric residue) fall to the bottom of the column and pass through a second heat exchanger prior to treatment in a vacuum distillation column. Finally, Bitumen is obtained by vacuum distillation or vacuum flashing of atmospheric residue from the vacuum distillation column. This is "straight run bitumen”. This process is called bitumen production by straight run vacuum distillation.
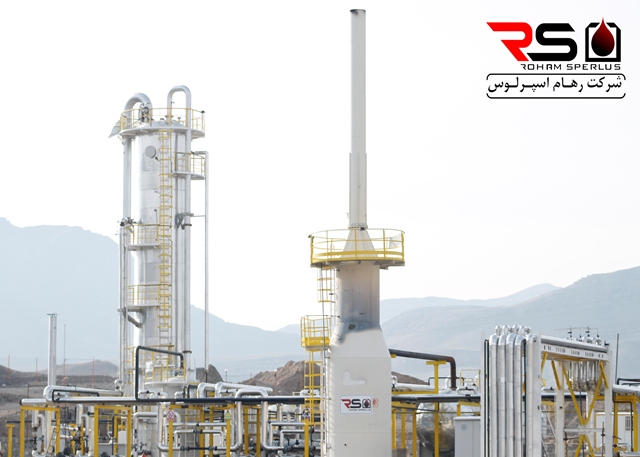
An alternative method of bitumen production is by precipitation from residual fractions by propane or butane-solvent deasphalting. The bitumen thus obtained has properties which derive from the type of crude oil processed and from the mode of operation in the vacuum unit or in the solvent deasphalting unit. The grade of the bitumen depends on the amount of volatile material that remains in the product: the smaller the amount of volatiles, the harder the residual bitumen.
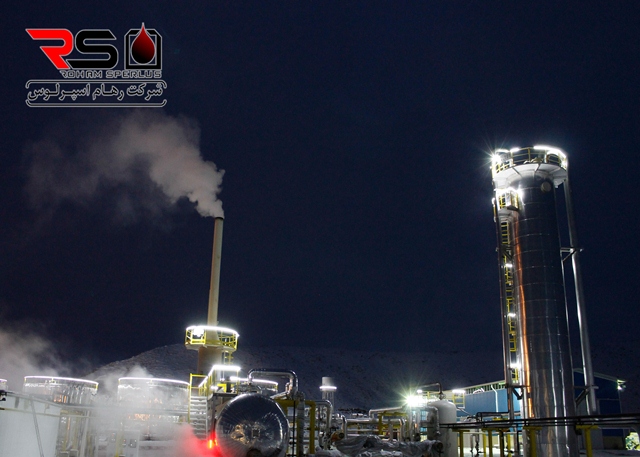
Specialists in bitumen view bitumen as an advanced and complex construction material, not as a mere by-product of the oil refining process.
Air Blowing
The properties of bitumen can be modified by air blowing in batch and continuous processes. On the other hand, the preparation of bitumen in liquid form by blending (cutting back) bitumen with a petroleum distillate fraction is customary and is generally accomplished in tanks equipped with coils for air agitation or with a mechanical stirrer or a vortex mixer. Air is heated up to 150–250°C and introduced at the bottom of a blowing column. It then migrates through the bitumen to the top of the column. The chemical reactions result in bitumen with a different mixture of molecular structures. Catalysts can influence this process.
Blown bitumen has more and stronger molecular interactions than the original bitumen and is therefore more cohesive. Blowing causes the softening point to increase and the penetration to decrease. However, the increase in softening point is usually more than the decrease in penetration. This means that blowing reduces the temperature susceptibility of bitumen. The effectiveness of blowing depends largely on the original bitumen (i.e. the original mixture of molecular structures). With respect to the composition, generally the amount of saturates do not change, the amount of aromates decreases because some oxidized aromates behave like resins, the amount of asphaltenes increases due to trans-formation of some resins and the total amount of resins stays the same.
When bitumen is strongly blown it becomes so cohesive that the adhesive properties become so poor that it is not suited for asphalt applications anymore. Therefore, only semi-blown bitumen is suited for asphalt applications. Semi-blown bitumen can have both improved cohesion and improved adhesion..